雙螺桿熱熔擠出機是高分子材料加工(如塑料共混、造粒、反應擠出)的核心設備,其運行穩定性直接影響產品質量與生產效率。由于長期處于高溫(150 - 350℃)、高壓(螺桿壓力可達20 - 50MPa)及高剪切環境,設備的維護保養與故障排除需結合機械結構、熱力學特性及工藝需求進行系統性管理。以下從維護保養規范與常見故障處理兩方面展開詳細分析。
??一、雙螺桿熱熔擠出機的維護保養規范??
??1. 日常操作維護:預防性管理的關鍵??
日常維護是減少設備故障的基礎,需在每次開機前、運行中及停機后進行標準化操作。
??開機前檢查??
??潤滑系統??:檢查齒輪箱、軸承座的潤滑油液位(油標中線以上),油質需清澈無雜質(若發黑或含金屬顆粒需立即更換);手動盤車確認螺桿轉動靈活,無卡滯異響。
??加熱系統??:檢查加熱圈絕緣性能(用萬用表測量電阻值,正常>10MΩ),確認溫控儀表設定值與工藝要求一致(誤差<±2℃);預熱階段需緩慢升溫(升溫速率≤50℃/h),避免熱應力導致機筒變形。
??進料系統??:清理料斗內殘留物料(防止結塊堵塞),檢查強制喂料器的螺桿與皮帶傳動是否正常,避免進料不均引發螺桿扭矩波動。
??運行中監控??
??溫度穩定性??:通過溫控儀表實時監測機筒各段溫度(如加料段、壓縮段、均化段),波動范圍需控制在±3℃內;若某段溫度持續偏高(超過設定值5℃以上),需檢查加熱圈是否局部短路或冷卻水路是否堵塞。
??壓力與扭矩??:觀察擠出機主電機電流(正常范圍為額定值的60% - 80%)及壓力傳感器數據(螺桿壓力≤40MPa),若電流驟增或壓力波動劇烈,可能因物料塑化不良或螺桿磨損導致。
??物料狀態??:通過視窗觀察熔體流動性(應均勻、無氣泡或未熔顆粒),若出現“架橋”(物料在料斗內堆積不下落)或“過熱碳化”(熔體發黃、有焦味),需及時調整進料速度或停機清理。
??停機后保養??
??清機操作??:生產不同配方物料時需清機(避免交叉污染),先排空機筒內剩余物料,再用高粘度硅油或專用清洗料(如PP清洗料)以低速(螺桿轉速≤10rpm)擠出,直至熔體無雜質;高溫段機筒需持續保溫(溫度≥180℃)防止殘留物料固化。
??冷卻系統維護??:關閉加熱系統后,啟動冷卻水循環(流量≥2m³/h),帶走機筒與螺桿殘余熱量;檢查冷卻水管路是否漏水(重點檢查法蘭連接處及軟管接頭),避免水滲入電氣柜引發短路。
??表面清潔??:用軟布擦拭設備表面(禁用鋼絲球或硬質刷子),清除油污與粉塵;拆卸防護罩檢查內部是否有異物(如金屬屑、塑料碎片),防止進入傳動系統。
??2. 定期深度保養:延長設備壽命的核心??
定期保養需根據設備運行時長(通常以2000 - 3000小時為周期)進行系統性維護,重點關注易損件與關鍵部件。
??螺桿與機筒的檢測與修復??
??磨損檢測??:拆卸螺桿后,用千分尺測量螺紋外徑(重點檢查壓縮段與均化段),磨損量>0.5mm需修復或更換;機筒內孔用內徑千分表檢測,圓度誤差>0.1mm或表面粗糙度Ra>1.6μm時需鏜孔修復。
??表面處理??:輕微磨損的螺桿可采用等離子噴涂(涂層材料為WC - Co硬質合金)或激光熔覆修復,恢復尺寸精度(涂層厚度0.2 - 0.5mm);機筒內壁若出現劃痕或腐蝕坑,需通過珩磨加工(表面粗糙度Ra≤0.8μm)提升光潔度。
??傳動系統的維護??
??齒輪箱??:更換齒輪油(ISO VG150或VG220,根據工況選擇),清洗磁性濾網(清除金屬磨屑);檢查齒輪嚙合間隙(側隙≤0.1mm,頂隙≤0.2mm),若齒面出現點蝕或膠合需更換齒輪組。
??軸承與密封件??:拆卸軸承座檢查滾子與內外圈磨損情況(若出現麻點或剝落需更換);更換機械密封件(如機筒與螺桿間的唇形密封圈),確保密封面無劃痕(密封壓力≥0.3MPa)。
??加熱與冷卻系統的檢修??
??加熱圈??:檢測功率穩定性(用功率分析儀測量,偏差<5%),更換老化絕緣層(云母片或陶瓷纖維);校準溫控儀表(與標準溫度計對比,誤差<±1℃)。
??冷卻水路??:清洗過濾器(清除水垢與雜質),檢測水泵揚程(≥0.3MPa)與流量(≥設計值的90%);對長期使用的銅管或不銹鋼管路進行渦流探傷(檢測壁厚減薄量,減薄>20%需更換)。
??3. 長期停機的特殊保養??
若設備需停機超過1個月,需采取防銹、防潮措施:
拆卸螺桿與機筒,涂抹防銹油(如二硫化鉬鋰基脂)后包裹塑料薄膜;
清空齒輪箱與液壓油箱,注入保護油(如含緩蝕劑的礦物油);
關閉電氣柜門,放置干燥劑(如硅膠包)并定期更換(每2周一次)。
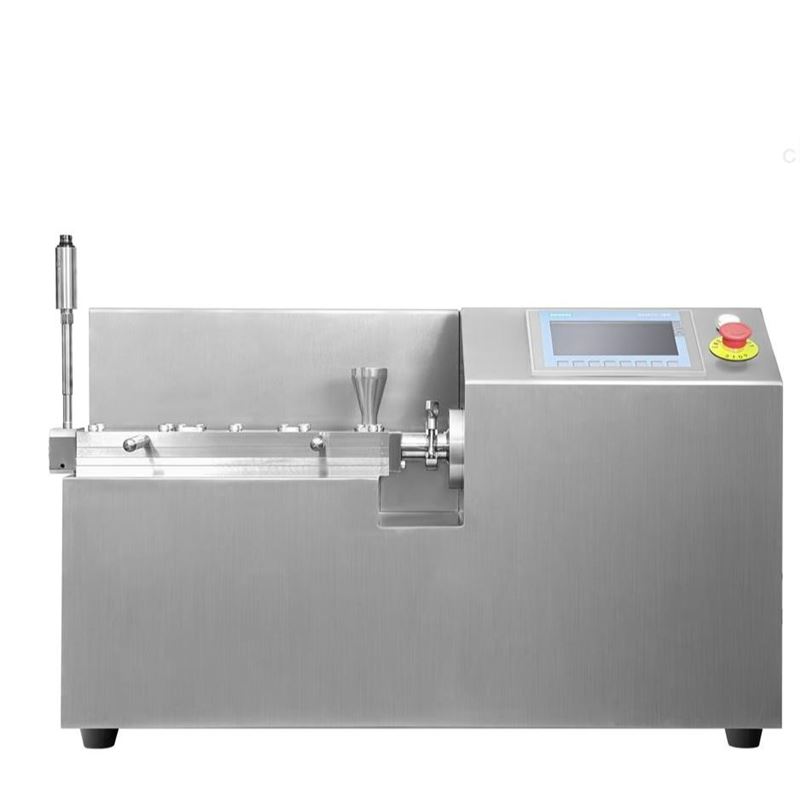
??二、雙螺桿熱熔擠出機的常見故障與排除方法??
??1. 機械類故障:傳動與結構問題??
??故障現象:螺桿扭矩異常升高(電機電流驟增)??
??可能原因??:物料塑化不良(如含水分或未干燥)、螺桿與機筒間隙過小(磨損后未調整)、異物進入螺槽(如金屬雜質)。
??排除方法??:檢查進料物料的含水率(需<0.02%),增加烘干時間(如80℃熱風干燥4小時);拆卸螺桿與機筒,測量間隙(正常值為0.1 - 0.3mm),若間隙<0.1mm需更換螺桿或修復機筒;檢查料斗篩網是否破損,加裝磁力架(吸附金屬顆粒)。
??故障現象:齒輪箱異響(周期性撞擊聲)??
??可能原因??:齒輪磨損(齒面點蝕或膠合)、軸承損壞(滾子破裂)、潤滑不足(油量不足或油質差)。
??排除方法??:停機后拆開齒輪箱蓋,檢查齒輪嚙合面(若有點蝕深度>0.1mm需更換齒輪組);拆卸軸承座,用聽診器檢測滾子轉動聲音(若出現“沙沙”聲需更換軸承);補充齒輪油至油標中線以上,更換老化濾芯。
??2. 熱力學類故障:溫度與壓力異常??
??故障現象:機筒某段溫度失控(持續升高或無法升溫)??
??可能原因??:加熱圈局部短路(絕緣層破損)、溫控儀表故障(傳感器漂移)、冷卻水路堵塞(水管結垢或閥門未開)。
??排除方法??:用萬用表測量加熱圈電阻值(若<5MΩ需更換);校準溫控儀表(與標準熱電偶對比,誤差>±3℃需調整或更換);檢查冷卻水管路(用高壓水槍沖洗過濾器,清除水垢)。
??故障現象:熔體壓力波動大(壓力表指針頻繁擺動)??
??可能原因??:螺桿轉速不穩定(變頻器故障)、物料進料不均(料斗架橋或喂料器故障)、機筒排氣口堵塞(揮發分無法排出)。
??排除方法??:檢查變頻器輸出頻率(正常波動范圍<±2Hz),重啟或更換變頻器;清理料斗內結塊物料(用木棒輕敲內壁),檢查強制喂料器皮帶張力(張緊力≥50N);拆卸機筒排氣口濾網(清除塑料熔體殘留)。
??3. 工藝類故障:產品質量問題??
??故障現象:擠出制品表面粗糙(有氣泡或條紋)??
??可能原因??:物料塑化不充分(溫度偏低或螺桿剪切不足)、熔體中含氣泡(物料含水分或揮發分)、模具溫度不均(冷卻不充分)。
??排除方法??:提高機筒溫度(如加料段提高10 - 15℃),調整螺桿轉速(增加剪切強度);檢查物料干燥工藝(如PET需在150℃下干燥4小時);清理模具冷卻水道(確保水流均勻,溫差<5℃)。
??故障現象:制品顏色不均(出現色斑或條紋)??
??可能原因??:色母粒分散不良(螺桿混合能力不足)、加料順序錯誤(色母粒未與基料充分預混)、機筒內壁殘留舊顏色物料。
??排除方法??:更換高剪切螺桿元件(如捏合塊或齒形盤),提高混合效率;采用預混工藝(色母粒與基料按比例在高速混合機中攪拌10分鐘);清機(用清洗料擠出至熔體無色差)。
??三、維護保養與故障排除的核心原則??
??預防為主??:通過日常巡檢與定期保養降低故障發生率,避免“帶病運行”;
??數據驅動??:記錄溫度、壓力、電流等關鍵參數的歷史數據(如建立Excel臺賬),通過趨勢分析預判潛在問題;
??專業操作??:故障排除需結合設備原理與工藝知識,避免盲目拆卸(如螺桿拆卸需使用專用工具,防止螺紋損傷)。
??結語??
雙螺桿熱熔擠出機的維護保養與故障排除是保障其高效運行的關鍵環節。通過標準化的日常維護、周期性的深度保養及快速精準的故障處理,可顯著延長設備壽命、提升產品質量穩定性,并降低生產成本。未來,隨著智能化監測技術(如在線磨損檢測傳感器、AI故障預測模型)的應用,擠出機的維護管理將向更高效、更精準的方向發展。